Characteristics and selection of different powder metallurgy UKO Blog
Powder metallurgy is widely used, and there are many kinds of materials used. How to choose the right powder metallurgy material is very important for a metallurgical factory like us, as well as for customers who need to buy metal mold tools. Now I will analyze the characteristics and suitable fields of different powder metallurgy for you.
Powder metallurgy antifriction material is also called sintering antifriction material. It is prepared by immersing lubricating oil in the pores of the material or adding friction-reducing agent or solid lubricant in the material composition. The friction coefficient between the surface of the material is small, so it has long service life and high reliability under the condition of limited lubricating oil; under the condition of dry friction, it has a self-lubricating effect depending on the lubricant contained in itself or on the surface. It is widely used in bearing, supporting a bush, or face seal.
Powder metallurgy porous materials, also known as porous sintered materials. It is made of spherical or irregular shaped metal or alloy powder by molding and sintering. The pores in the material are crisscross and connected with each other. Generally, the porosity is 30% – 60% and the pore size is 1-100 μ M. It has good permeability, thermal conductivity, high temperature and low-temperature resistance, thermal shock resistance, and medium corrosion resistance. It is used to manufacture filters, porous electrodes, fire extinguishing devices, antifreeze devices, etc.
Powder metallurgy structural materials, also known as sintered structural materials. It can bear tension, compression, torsion, and other loads, and can work under friction and wear conditions. Due to the existence of residual pores in the material, its ductility and impact value is lower than those of castings and forgings with the same chemical composition.
Powder metallurgy friction materials, also known as sintered friction materials. It consists of three parts: base metal, lubricating component, and friction component. It has high friction coefficient, can quickly absorb kinetic energy, brake and transmission speed is fast, wear is small; high strength, high-temperature resistance, good thermal conductivity; good anti-seizing property, corrosion resistance, less affected by grease and moisture. It is mainly used for manufacturing clutch and brake.
Powder metallurgy mold materials, including cemented carbide, powder metallurgy high-speed steel, and so on. The latter has uniform structure, fine grain, and no segregation, better toughness and wear resistance, smaller heat treatment deformation, and longer service life than cast high-speed steel. It can be used to make blanks for cutting tools, dies, and parts.
PM high-temperature materials include PM superalloys, refractory metals and alloys, cermet, dispersion strengthened, and fiber-reinforced materials. It is used to manufacture turbine disk, nozzle, blade, and other high-temperature resistant parts. UKO also used cermet to make cermet CNC inserts.
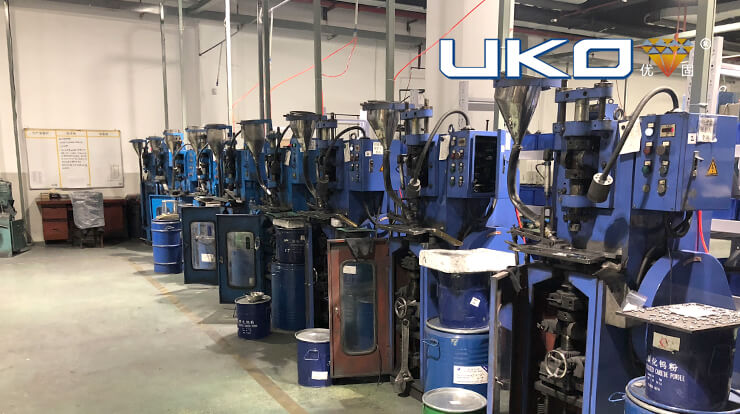
UKO mainly produces and sells materials in the following two categories: powder metallurgy mold materials and powder metallurgy high-temperature materials, including cemented carbide, high-speed steel, and cermet. Our products include CNC cutting tools, molds, and parts for woodworking and metal processing.